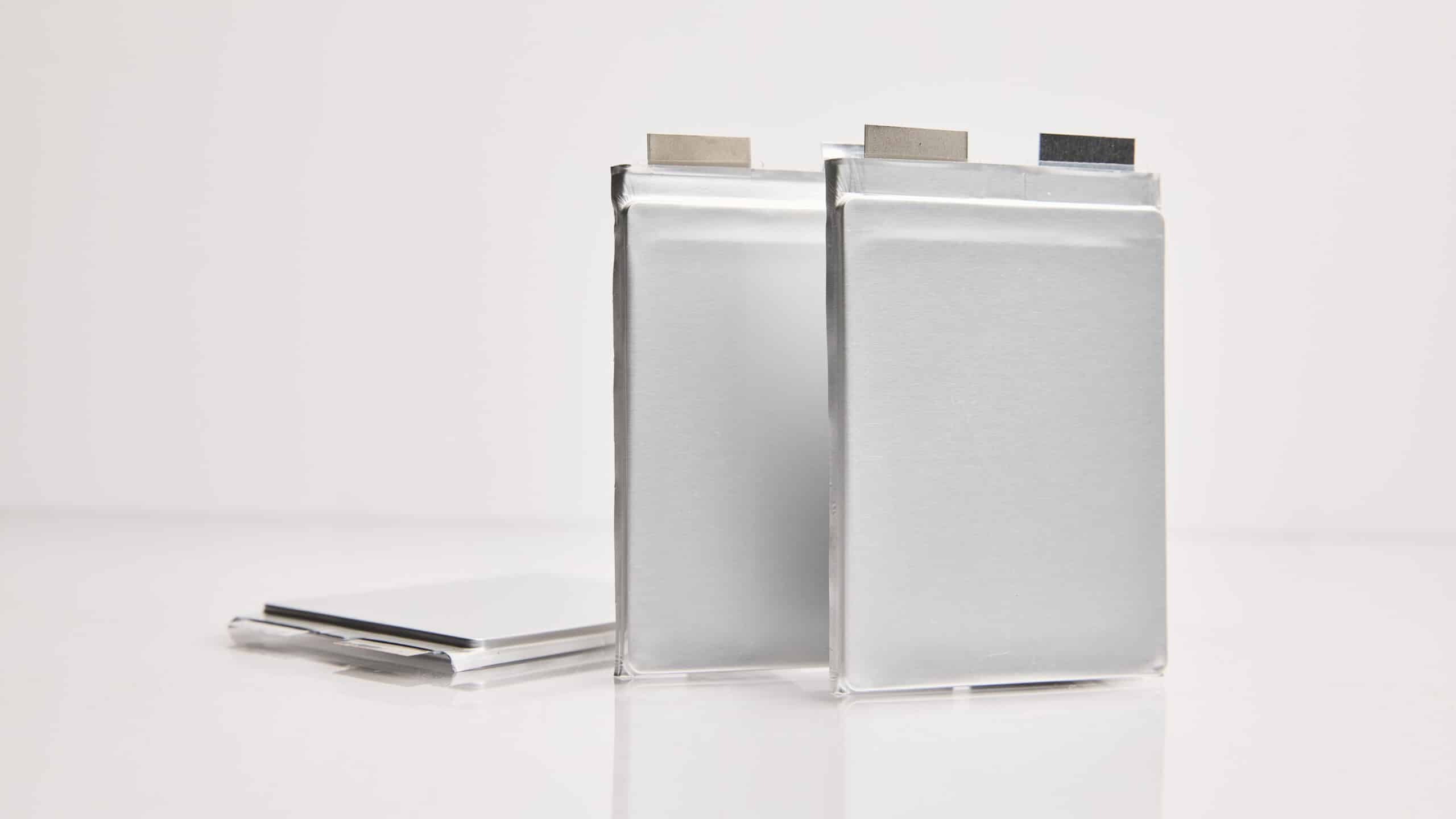
Our Strategic Blueprint
I took on the CEO role last year because I see QuantumScape as the global leader in solid state battery technologies with an ability to revolutionize energy storage and create tremendous shareholder value in the process.
Rechargeable lithium-metal batteries have been the subject of intense research for decades, and today they seem closer than ever to reaching the marketplace. But why are lithium-metal anodes such a sought-after goal in battery science? Here, we’ll try to shed some light on the excitement around lithium metal.
Many elements can be used in rechargeable batteries. So, what is it about lithium that makes it so attractive for electric vehicles?
When it comes to choosing a material for a lithium-based battery anode, there are various options.[4] The most important characteristics of an anode material are its capacity and voltage, which together dictate its overall energy storage capability. When it comes to anodes for EV batteries, there are three leading contenders: graphite, silicon and lithium metal. Lithium metal is the winner in energy density,[5] but each has its challenges.
However, graphite has a relatively low capacity, so it can’t pack many lithium ions into a given space. This means graphite-based anodes offer poor energy density, resulting in a limited driving range in EVs. There is also a limit to how fast lithium can intercalate into graphite, a critical bottleneck that constrains fast vehicle charging speeds.[7]
Graphite also reacts with liquid electrolytes in conventional lithium-ion batteries. This reaction creates a stable solid-electrolyte interphase (SEI) layer, which protects the bulk of the graphite from contacting the electrolyte. Capacity loss from side reactions, while still an issue, is less of a problem with graphite than other materials like silicon. This relative stability is what makes graphite so popular as an anode host, despite its other drawbacks. However, these side reactions still consume lithium, reducing battery capacity and creating side products that make it harder for lithium to move in and out of the anode. These two effects reduce both the power the battery can deliver and the energy it can store, meaning slower charging, slower acceleration, and lower driving range.
This cracking process means that the SEI layer is continually destroyed and reformed over many cycles, increasing the rate at which side reactions consume the lithium in the battery. This causes the battery to lose capacity and increases cell resistance, and therefore reduces its voltage. This means batteries based on silicon anodes tend to lose energy storage capability rapidly.
Adapted from Choi et al. Nat Rev Mater 1, 16013 (2016). https://doi.org/10.1038/natrevmats.2016.13
There are a few workarounds for this problem, but all have tradeoffs. The silicon may have lithium added to offset the capacity losses, known as pre-lithiation, but this adds to cost and makes manufacturing more difficult. The batteries can be kept under enormous pressure to prevent the silicon from cracking, but the mass of the pressure apparatus offsets much of the benefit the silicon provides in the first place. Silicon nanostructures can be engineered to overcome these challenges, but these are more complex and expensive than simple graphite, and lower the theoretical capacity advantage of using silicon in the first place. Lastly, silicon pays a voltage penalty that reduces cell energy. Due to these drawbacks, silicon is usually mixed with graphite, and typically only in small amounts.
Pure lithium metal tends to form dendrites, which can diminish a battery’s safety and service life. Many electrolyte materials, such as liquids, solid polymers, and sulfides, have not been shown to prevent dendrites.
Lithium metal is also highly reactive, which poses a problem for sulfides, liquids, and solid polymers. This reactivity consumes lithium, and so the battery must have extra lithium added in the form of a thin lithium foil to function. Unfortunately, lithium foil introduces a tradeoff between volumetric energy density (the amount of energy stored in a given volume) and cost. Very thin lithium foils are expensive to produce and difficult to handle, and thicker lithium foils eliminate the volumetric energy density advantage that motivates the switch from graphite.
Lithium foils also make the dendrite problem harder to solve. Manufactured foil always has slight impurities or variations in the material itself, which intensifies lithium plating at specific points, and catalyzes the growth of dendrites.
QuantumScape’s battery technology is designed to address the fundamental challenges of lithium metal. Our ceramic solid-electrolyte separator has demonstrated the ability to resist dendrites at rates of power relevant for EVs. Our separator offers very good stability with lithium metal, which reduces lithium consumption to side reactions and contributes to excellent Coulombic efficiency. This stability means extra lithium isn’t required, and cells can be manufactured without an anode. Instead, as the cell is charged, lithium is drawn from the cathode through the ceramic solid-electrolyte separator and plates on the anode as pure lithium metal. This process ensures that the anode is free of impurities and eliminates the material and manufacturing costs required to produce and integrate lithium foil into the cell.
Instead of adding expensive extra anode materials, QuantumScape’s technology makes better batteries by simplifying the cell design. Eliminating the need for graphite, silicon, or lithium foil offers a pathway for QuantumScape’s technology to increase energy density and improve vehicle range while simultaneously enabling 15-minute fast charging. We believe our solid-state lithium-metal battery technology represents the most promising pathway to next-generation battery performance.
[1]Very roughly, the abundance of lithium in Earth’s crust is ~20 parts per million (ppm) by mass and ~70ppm by number of atoms. [Source: https://en.wikipedia.org/wiki/Abundances_of_the_elements_(data_page)] The number of atoms in the Earth is approximately 1.33 x 1050 [Source: https://education.jlab.org/qa/mathatom_05.html]. The Earth’s crust is ~1% of volume of Earth [Source: https://en.wikipedia.org/wiki/Earth%27s_crust)]. The density of the core and crust are different, but for an order-of-magnitude estimate, assume that the crust contains 1% of the atoms in the earth. Therefore, there are ~1 x 1044 atoms of lithium in the crust. That lithium represents 2 x 1021 Ah worth of battery capacity (8 x 1021 Wh at 4V), assuming half of the lithium ions in a battery are active. If the average electric vehicle battery pack is 75 kWh, this translates to 100 quadrillion (1 x 1017) EVs. Assuming ~100M cars sold per year, that amounts to one billion years’ worth of production. Even if only one in a million lithium atoms can be used, that still amounts to a thousand years of production.
[2] When estimated on a per-atom basis: https://en.wikipedia.org/wiki/Lithium#/media/File:Elemental_abundances.svg
[3] For more information on lithium mining in the U.S.: https://medium.com/prime-movers-lab/does-the-u-s-have-enough-lithium-to-support-the-growing-ev-market-d73a44a969e5
[4] We reviewed some of the popular cathode options in an earlier article.
[5] In theory, silicon has a slightly higher volumetric capacity than lithium metal: theoretical volumetric capacity of silicon is 2190 mAh/cm3 vs 2062 mAh/cm3 for lithium metal. But in real-world silicon anodes, a large fraction of volume is filled with carbon, polymer, liquid electrolyte, or other materials, so the practical volumetric capacity is much lower. In contrast, QuantumScape’s anode-free lithium metal architecture is pure lithium metal with no excess, so there is no wasted space. In addition, silicon pays a voltage penalty relative to lithium metal, so higher volumetric capacity does not translate to higher energy. Gravimetric energy density is higher for lithium metal regardless, since there is no additional weight from silicon atoms.
[6] For more details on dendrites, see our blog on sulfides: https://www.quantumscape.com/resources/blog/the-problem-with-sulfides/
[7] For more information on fast charging, see our white paper: https://www.quantumscape.com/resources/blog/white-paper-a-deep-dive-into-quantumscapes-fast-charging-performance/
[8] The specific capacity of graphite is 372 mAh/g versus 3600 mAh/g for silicon.
[9] The specific capacity of lithium metal is 3863 mAh/g.
Forward-Looking Statements
This article contains forward-looking statements within the meaning of the federal securities laws and information based on management’s current expectations as of the date of this current report. All statements other than statements of historical fact contained in this article, including statements regarding the future development of QuantumScape’s battery technology, the anticipated benefits of QuantumScape’s technologies and the performance of its batteries, and plans and objectives for future operations, are forward-looking statements. When used in this current report, the words “may,” “will,” “estimate,” “pro forma,” “expect,” “plan,” “believe,” “potential,” “predict,” “target,” “should,” “would,” “could,” “continue,” “believe,” “project,” “intend,” “anticipates” the negative of such terms and other similar expressions are intended to identify forward-looking statements, although not all forward-looking statements contain such identifying words.
These forward-looking statements are based on management’s current expectations, assumptions, hopes, beliefs, intentions, and strategies regarding future events and are based on currently available information as to the outcome and timing of future events. These forward-looking statements involve significant risks and uncertainties that could cause the actual results to differ materially from the expected results. Many of these factors are outside QuantumScape’s control and are difficult to predict. QuantumScape cautions readers not to place undue reliance upon any forward-looking statements, which speak only as of the date made. Except as otherwise required by applicable law, QuantumScape disclaims any duty to update any forward-looking statements. Should underlying assumptions prove incorrect, actual results and projections could differ materially from those expressed in any forward-looking statements. Additional information concerning these and other factors that could materially affect QuantumScape’s actual results can be found in QuantumScape’s periodic filings with the SEC. QuantumScape’s SEC filings are available publicly on the SEC’s website at www.sec.gov.
I took on the CEO role last year because I see QuantumScape as the global leader in solid state battery technologies with an ability to revolutionize energy storage and create tremendous shareholder value in the process.
QuantumScape’s planned first commercial product, QSE-5, is a ~5 amp-hour cell designed to meet the requirements of automotive applications. Here, we’ll walk through the various elements of the cell specifications and explain some of the complexities behind the seemingly simple metric of energy density.
I took on the CEO role last year because I see QuantumScape as the global leader in solid state battery technologies with an ability to revolutionize energy storage and create tremendous shareholder value in the process.
QuantumScape’s planned first commercial product, QSE-5, is a ~5 amp-hour cell designed to meet the requirements of automotive applications. Here, we’ll walk through the various elements of the cell specifications and explain some of the complexities behind the seemingly simple metric of energy density.
Privacy Policy | Terms of Use
© 2025 QuantumScape Battery, Inc.
1730 Technology Drive, San Jose, CA 95110
info@quantumscape.com
Pamela Fong is QuantumScape’s Chief of Human Resources Operations, leading people strategy and operations, including talent acquisition, organizational development and employee engagement. Prior to joining the company, Ms. Fong served as the Vice President of Global Human Resources at PDF Solutions (NASDAQ: PDFS), a semiconductor SAAS company. Before that, she served in several HR leadership roles at Foxconn Interconnect Technology, Inc., a multinational electronics manufacturer, and NUMMI, an automotive manufacturing joint venture between Toyota and General Motors. Ms. Fong holds a B.S. in Business Administration from U.C. Berkeley and a M.S. in Management from Stanford Graduate School of Business.