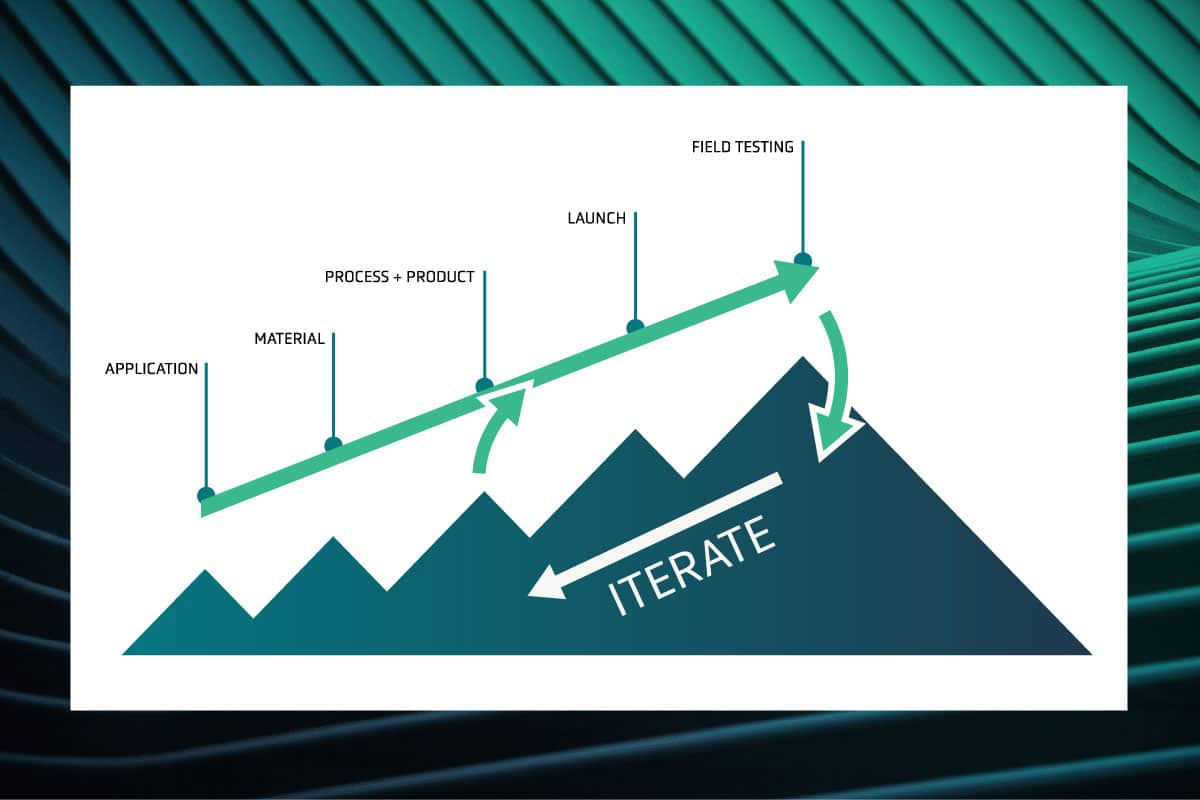
Amplifying Innovation: The QS approach to technology development
Bringing a new technology to market can seem mysterious from the outside. Headlines tout “breakthroughs” that never materialize, leaving people skeptical. And yet, technology does advance steadily forward – faster computers, cheaper renewables, and better EVs arrive every year. So what separates hype from true innovation?